Gea Heat Exchanger Plate are essential components that play a crucial role in the efficient operation of heat exchangers. These Gea Heat Exchanger Plate are designed to replace damaged or worn-out plates in GEA heat exchangers, ensuring the continued performance and longevity of the equipment. In this article, we will explore the importance of PHE spare plates for GEA, their features, benefits, and the factors to consider when selecting the right spare plates. Phe Plate For Gea,Gea Phe Heat Exchanger Plate,Gea Heat Exchanger Plate,Gea Phe Plate Dongguan Runfengda F&M Co., Ltd , https://www.rfdphe.com
Gea Heat Exchanger Plate are widely used in various industries, including HVAC, chemical processing, power generation, and food and beverage. They are used to transfer heat from one fluid to another, without the fluids coming into direct contact. This transfer of heat is facilitated by the use of plates, which are arranged in a parallel configuration with alternating hot and cold fluids flowing through them. The Gea Heat Exchanger Plate provide a large surface area for efficient heat transfer, while the design allows for easy maintenance and cleaning.
Over time, the Gea Heat Exchanger Plates in a heat exchanger can become damaged or worn-out due to factors such as corrosion, fouling, or mechanical stress. When this happens, the performance of the heat exchanger is compromised, leading to reduced efficiency and increased energy consumption. In such cases,Gea Heat Exchanger Plate is necessary to replace the damaged plates with spare plates to restore the heat exchanger's optimal performance.
PHE spare plates for GEA are specifically designed to meet the requirements of GEA heat exchangers. These plates are made from high-quality materials, such as stainless steel or titanium, to ensure durability and resistance to corrosion. They are also designed with precise dimensions and specifications to fit seamlessly into GEA heat exchangers, ensuring a proper seal and efficient heat transfer.
One of the key benefits of using Gea Heat Exchanger Plate is the cost savings they offer. By replacing damaged plates with spare plates, companies can avoid the need to invest in a completely new heat exchanger, which can be a significant expense. Instead, they can simply replace the damaged plates, extending the lifespan of the heat exchanger and maximizing the return on investment.
Another advantage of using PHE spare plates for GEA is the minimal downtime required for replacement. Heat exchangers are critical components in many industrial processes, and any downtime can result in costly production delays. By having spare plates readily available, companies can quickly replace the damaged plates and minimize the downtime associated with maintenance and repair.
When selecting PHE spare plates for GEA, there are several factors to consider. Firstly, it is important to ensure that the spare plates are compatible with the specific model and size of the GEA heat exchanger. This can be determined by referring to the heat exchanger's technical specifications or consulting with the manufacturer.
Additionally, the material of the Gea Heat Exchanger Plate should be chosen based on the application and the fluids being processed. For example, in applications where corrosion is a concern, stainless steel or titanium plates may be preferred. The thickness and design of the plates should also be considered to ensure optimal heat transfer and efficiency.
Furthermore, it is advisable to source PHE spare plates from reputable manufacturers or suppliers. This ensures the quality and reliability of the spare plates, as well as access to technical support and expertise if needed. Reputable manufacturers often provide warranties or guarantees on their spare plates, giving customers peace of mind regarding their performance and durability.
In conclusion, PHE spare plates for GEA are essential components that ensure the efficient operation of heat exchangers. These Gea Heat Exchanger Plates are designed to replace damaged or worn-out plates, thereby restoring the heat exchanger's performance and extending its lifespan. By selecting the right spare plates and partnering with reputable manufacturers or suppliers, companies can enjoy the benefits of cost savings, minimal downtime, and optimal heat transfer in their GEA heat exchangers.
All Geared Lathe Machine: A Comprehensive Overview
The all geared lathe machine is a fundamental tool in the world of machining and metalworking. Known for its precision, power, and adaptability, this type of lathe is widely used across industries such as automotive, aerospace, tool manufacturing, and general engineering. Its ability to shape, cut, and form various materials—like metal, plastic, and wood—makes it an essential asset in any workshop.
In this article, we’ll take a closer look at the importance of all geared lathe machines, how they function, and the different types available in the market. We'll focus on four main categories: Light Duty Lathe Machines, Medium Duty Lathe Machines, Heavy Duty Lathe Machines, and Extra Heavy Duty Lathe Machines.
**What is an All Geared Lathe Machine?**
An **all geared lathe machine** is a mechanical device designed to rotate a workpiece against cutting tools to perform operations like cutting, sanding, knurling, drilling, and turning. What sets it apart from traditional lathes is its gear-driven transmission system, which replaces belt-driven mechanisms. This design offers greater efficiency, precision, and the ability to handle heavier loads with ease.
Unlike conventional lathes that rely on belt adjustments for speed control, all geared lathes allow users to change speed by engaging different gear combinations. This provides more control over the machining process and ensures a higher level of accuracy in the final product.
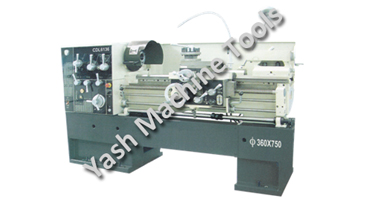
**Key Features of All Geared Lathe Machines**
- **High Precision**: The gear-driven mechanism ensures accurate machining results.
- **Versatility**: Suitable for a wide range of tasks including threading, facing, and turning.
- **High Speed and Power**: Gears allow for speed changes without losing torque, making them ideal for both light and heavy-duty work.
- **Durability**: Built with strong materials to ensure long-lasting performance under demanding conditions.
- **Low Maintenance**: With fewer moving parts compared to belt-driven models, maintenance is minimal.
**Types of All Geared Lathe Machines**
All geared lathes are categorized based on their size, capacity, and intended use. The four main types are:
1. **Light Duty Lathe Machine**
2. **Medium Duty Lathe Machine**
3. **Heavy Duty Lathe Machine**
4. **Extra Heavy Duty Lathe Machine**
Each type is suited for specific applications, depending on the workload and required precision.
**1. Light Duty Lathe Machine**
A **light duty lathe machine** is ideal for small-scale tasks and hobbyists. It’s perfect for precise machining where large material removal isn't needed. These machines are compact, easy to operate, and energy-efficient.
**Key Features:**
- Compact and lightweight
- Low power consumption
- Excellent for detailed work on small components
- Simple controls for user-friendly operation
**Applications:**
- Small-scale metalworking
- Crafting decorative pieces
- Education and training
- Repair and maintenance of small parts
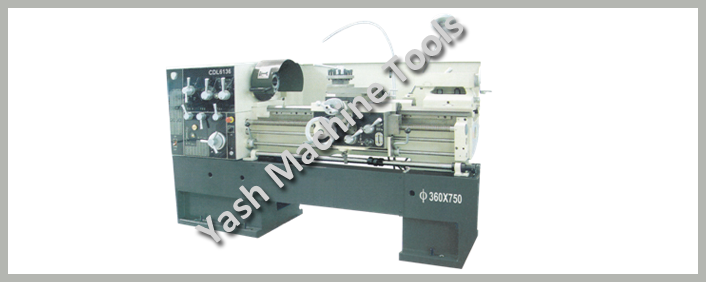
**2. Medium Duty Lathe Machine**
A **medium duty lathe machine** offers a balance between power and versatility. It's suitable for general-purpose machining tasks and can handle a variety of metals and materials.
**Key Features:**
- Increased power and stability
- Larger bed length for bigger workpieces
- Versatile for both light and moderate tasks
- Better precision and durability
**Applications:**
- General machining in small to medium workshops
- Production of machine parts and automotive components
- Metalworking in repair and maintenance
- Customized small-batch production
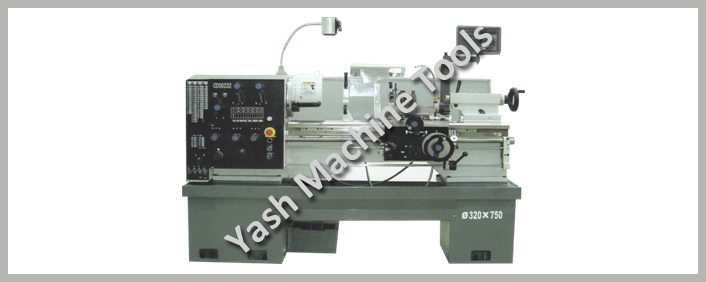
**3. Heavy Duty Lathe Machine**
For industrial applications that require strength and precision, the **heavy duty lathe machine** is the go-to choice. These machines are built to handle large workpieces and tough materials.
**Key Features:**
- High torque and power
- Long bed lengths and larger spindle bores
- Enhanced stability and durability
- Advanced features like digital readouts and automatic feeds
**Applications:**
- Manufacturing large machine parts
- Machining shafts, cylinders, and pipes
- Construction equipment production
- Large-scale industrial manufacturing
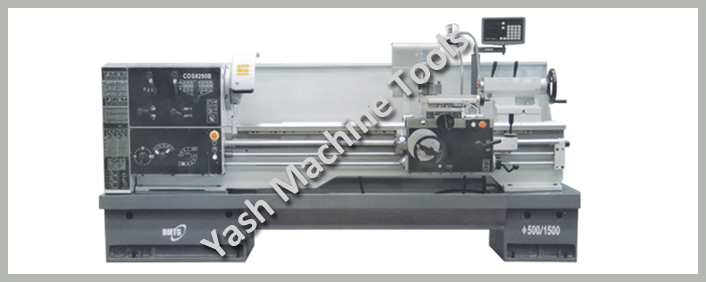
**4. Extra Heavy Duty Lathe Machine**
At the top of the scale, the **extra heavy duty lathe machine** is designed for extreme industrial use. These machines are built to handle the heaviest and most complex machining tasks with unmatched precision.
**Key Features:**
- Maximum power and load capacity
- Superior stability and precision
- Customizable for specialized applications
- Designed for large and heavy workpieces
**Applications:**
- Aerospace component manufacturing
- Shipbuilding
- Wind turbine part production
- Industrial machinery manufacturing
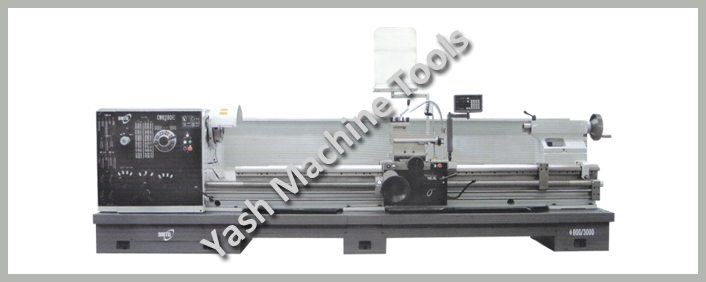
**Conclusion**
The all geared lathe machine is a vital tool in any machining or metalworking environment. Whether you're running a small workshop or managing a large industrial operation, there's a geared lathe machine that suits your needs. From light to extra heavy duty, each type offers unique advantages. Choosing the right one ensures efficiency, precision, and high-quality results in your machining projects. Investing in an all geared lathe machine is a smart decision that can boost productivity and deliver consistent, professional outcomes.